Real Results in the Field: How AutoCx Transforms Commissioning
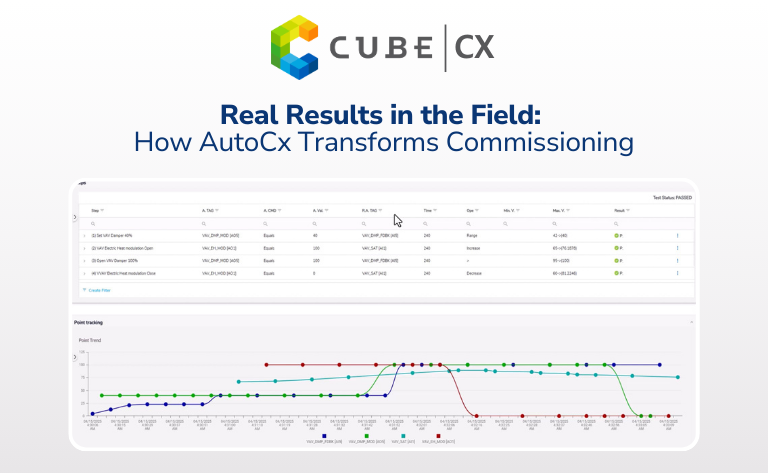
Commissioning can be complex, time-consuming, and resource-intensive — but what if it didn’t have to be?
Today, I want to walk you through a real-world example where CUBE-Cx and AutoCx helped a project team streamline their entire commissioning process, save time, reduce labor, and make smarter decisions — all without sending a technician on-site.
Let’s dive into how this happened.
The Project: A Large-Scale Hotel in Orlando
A high-end hotel complex in Orlando was nearing completion. The commissioning was being managed by one of our South Florida clients, and the scope was significant: hundreds of terminal units, all requiring functional testing and verification before occupancy.
Traditionally, this kind of project demands a heavy technician presence — walking floor after floor, opening ceilings, manually running tests, and documenting results.
But not this time.
Enter AutoCx: Automated, Intelligent Commissioning
Instead of deploying a team of techs across the site, the client used CUBE-Cx with AutoCx to perform 100% of the terminal unit testing digitally.
Every test was:
- Scheduled automatically
- Executed autonomously
- Logged and displayed in real-time
Technicians weren’t walking the building — the building was walking itself through commissioning.
Benefit #1: Time Saved, Labor Slashed
The most immediate impact? Massive time savings.
Instead of manually testing hundreds of devices, AutoCx ran every test remotely. The team could then focus only on the handful of devices that failed, rather than spending hours verifying equipment that was already working.
Benefit #2: Real-Time Visibility & First-Pass Succes
As results streamed in, a large percentage of the equipment passed on the first attempt.
CUBE-Cx’s intuitive dashboard displayed each pass/fail result visually, with successful tests in green and failed ones in red. That meant the team didn’t have to dig — they could instantly identify what needed attention and what didn’t.
Zooming In: Diagnosing a Real Failure
Let’s take a closer look at one of the units that failed.
Issue flagged: Cooling valve not opening
Here’s how AutoCx helped:
- The fan was commanded to run at 100% — √ Passed
- The valve was commanded to open — but instead of cooling, temperature increased
- Trend data revealed the valve was configured incorrectly (direct acting instead of reverse)
Because the test was backed by real trend data, the engineer didn’t have to guess — they could see exactly what went wrong.
Benefit #3: Fast, Remote Resolution
No site visit. No delay.
The engineer remotely accessed the controller, changed the valve’s configuration, and re-ran the test.
This time, it passed — and no technician had to step foot on-site.
Traditional Commissioning vs AutoCx: A Stark Contrast
Now imagine if this had been done the old way…
- The issue might not be found until the building was occupied
- A tech would have to report it manually
- An engineer might need to travel to the site
- The issue would be fixed, and a retest would be required
All of this consumes time, labor, and budget — and delays turnover.
The AutoCx Advantage: Why It Matters
With CUBE-Cx and AutoCx, commissioning becomes:
- Faster
- Smarter
- More cost-effective
- Scalable — even with limited staff
In a world where skilled labor is in short supply, automation isn’t just an upgrade — it’s a necessity.
Final Thoughts
This case is just one example of how CUBE-Cx is changing the game for commissioning teams.
By automating testing, surfacing actionable insights, and enabling remote resolution, AutoCx empowers your team to deliver results faster and more reliably — without the burnout.
Ready to transform the way you commission buildings?
We put together a short walkthrough video so you can experience the AutoCx difference for yourself. See it in action here!
Let’s make it happen — the smarter way.